<Bomi>
|
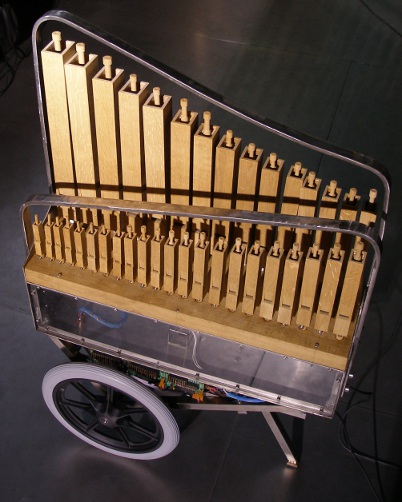
an automated organ gedeckt register
Godfried-Willem
RAES
2009-2010
|
The design of this musical robot started with an offer found on the August
Laukhuff website for a wooden 4-feet register perfectly suitable to complement
our <Bourdonola> robot, or to yield to an easy transportable organ module.
The sound was designed such as to be soft and gentle, but still pretty rich
in overtones and with a clear slightly spitting attack.
In the <Bomi> robot we designed around this register, the notes are switched
inside the windchest with conical electrical pallets, solenoid driven. Doing
so, we obtained velocity sensitivity for each individual note as well as individual
keypressure modulation. Global wind pressure control is possible over a wide
range, although as can be expected from flue pipes, tuning cannot be guaranteed
under extreme deviation from the normal pressure circumstances. The global pressure
control is mapped on midi controller 7, as it is related to the sound volume.
Maximum wind pressure is 65 mm watercolumn (= 6.5 mbar) and generated by a small
70 Watt Laukhuff Ventola-type organ blower driven by a programmable 3-phase
motor controller from Siemens. Air production is 1 cubic meter a minute. Normal
working pressure should be 45 mm watercolumn (4.5 mbar). Tuning is pretty much
stable in the range 40 to 50 mm H20. A manometer as well
as a thermometer are mounted on the windchest. A tremulant, using a softshift
solenoid valve on the wind inlet in the windchest, is also part of the design.
Its operation can be seen as we made the windchest transparent. The softshift
valve used here to steer a conical valve can be controlled with midi controller
1, however, its function is inverted such that for controller value zero, the
valve will be fully opened and for value 127 fully closed. The all notes off
command (controller 123) always resets this valve to the fully opened state.
The valve can very well be used for fast responding dynamic control as well
as for inflections.
The entire circuitry for this robot makes use of three fast
PIC controllers: Microchip PIC18F4625 - I/SP types. For each group of 14 notes,
a controller takes care of the midi input parsing and the note on/offs, mosfets
and conical valve solenoids. There is precise control over the note attack (the
velocity byte accompanying each note on command controlling the response speed
of the valves) as well as over windflow modulation during the sounding of a
note. This is implemented with polyphonic midi note aftertouch commands and,
on the processor level, by applying slow PWM to the hold voltages over the solenoids.
This is the principle:
It
is important to the user to know that the velocity byte in the midi note-on
command does not control sound volume, but only the way the pipes speak. It
is strictly an attack control. For detailed circuitry and board population,
we refer to the webpage of our <harmO> robot,
since it uses the same boards. The PIC firmware however is very different, since
here we implemented the PWM steering required for the key pressure control.
A fourth PIC microcontroller (a 18F2525 type) takes care of the steering of
the windvalve/tremulant as well as of the motor commands and the PWM for the
3-phase motor controller.
Description of the organ register:
Name: Gedaeckt, 4' - 37 stopped wooden pipes. (3 octaves)
Light colored oak wood is used for the pipes. The wood is left in its natural
and untreated state. The pipefeet have individual regulating screws. The pipes
are tightly fitted to the windchest using easily replaceable Teflon tape (PTFE).,
the same type as used in general plumbing. Since the instrument is designed
for transportation, the pipes are inserted deeper into the upperplate of the
windchest than usual in traditional organ building.
The scale used for the register is (scales in mm):
|
|
internal |
external |
pipe length |
pipe length from flue |
length of foot |
diameters
(20mm traject)
|
hole size |
conical valve |
note 55 |
g 0 |
37.0 x 49.0 |
50.0 x 63.0 |
460 mm |
400 mm |
60 |
14.5 - 17 |
10 |
24 |
note 56 |
g#0 |
35.5 x 47.0 |
49.0 x 61.0 |
435 mm |
378 mm |
60 |
14.5 - 17 |
10 |
24 |
note 57 |
a 0 |
33.5 x 45.0 |
47.0 x 59.0 |
414 mm |
355 mm |
60 |
14.5 - 17 |
10 |
24 |
note 58 |
a#0 |
33.0 x 43.5 |
46.0 x 58.0 |
392 mm |
336 mm |
60 |
14.5 - 17 |
10 |
24 |
note 59 |
b 0 |
31.0 x 42.0 |
45.0 x 56.0 |
370 mm |
313 mm |
60 |
14.5 - 17 |
10 |
24 |
note 60 |
c 1 |
29.0 x 41.0 |
43.0 x 54.0 |
340 mm |
280 mm |
60 |
14.5 - 17 |
9 |
24 |
note 61 |
c#1 |
28.5 x 38.7 |
42.0 x 50.5 |
324 mm |
267 mm |
60 |
14.5 - 17 |
9 |
24 |
note 62 |
d 1 |
27.0 x 37.5 |
40.0 x 50.0 |
305 mm |
250 mm |
60 |
14.5 - 17 |
9 |
24 |
note 63 |
d#1 |
26.5 x 36.0 |
38.5 x 48.5 |
290 mm |
237 mm |
50 |
13 - 15 |
8 /8.5 |
18 |
note 64 |
e 1 |
25.0 x 35.0 |
37.0 x 47.5 |
274 mm |
220 mm |
50 |
13 - 15 |
8.5 |
18 |
note 65 |
f 1 |
23.5 x 32.5 |
34.5 x 45.0 |
260 mm |
210 mm |
50 |
13 - 15 |
8.5 |
18 |
note 66 |
f#1 |
23.5 x 32.0 |
34.5 x 43.5 |
250 mm |
195 mm |
50 |
13 - 15 |
8.5 |
18 |
note 67 |
g 1 |
23.0 x 30.0 |
33.0 x 42.0 |
238 mm |
185 mm |
50 |
13 - 15 |
8.5 |
18 |
note 68 |
g#1 |
21.5 x 30.0 |
32.0 x 40.5 |
227 mm |
175 mm |
50 |
13 - 15 |
8.5 |
18 |
note 69 |
a 1 |
21.0 x 29.0 |
31.0 x 40.0 |
220 mm |
170 mm |
50 |
13 - 15 |
8.5 |
18 |
note 70 |
a#1 |
20.0 x 27.5 |
30.0 x 37.5 |
207 mm |
159 mm |
50 |
13 - 15 |
8.5 |
18 |
note 71 |
b 1 |
19.5 x 27.5 |
29.0 x 36.5 |
199 mm |
151 mm |
50 |
13 - 15 |
8.5 |
18 |
note 72 |
c 2 |
18.7 x 25.5 |
28.5 x 35.4 |
190 mm |
143 mm |
50 |
13 - 15 |
8 / 8.5 |
18 |
note 73 |
c#2 |
18.0 x 24.5 |
28.0 x 34.5 |
180 mm |
133 mm |
40 |
11 - 14 |
7 / 6.5 |
16 |
note 74 |
d 2 |
17.0 x 24.0 |
27.0 x 34.5 |
175 mm |
128 mm |
40 |
11 - 14 |
6.5 |
16 |
note 75 |
d#2 |
16.5 x 22.9 |
25.0 x 32.0 |
169 mm |
122 mm |
40 |
11 - 14 |
6.5 |
16 |
note 76 |
e 2 |
15.5 x 22.0 |
24.5 x 31.0 |
162 mm |
117 mm |
40 |
11 - 14 |
6.5 |
16 |
note 77 |
f 2 |
15.0 x 21.0 |
24.0 x 30.0 |
155 mm |
109 mm |
40 |
11 - 14 |
6.5 |
16 |
note 78 |
f#2 |
14.5 x 21.0 |
23.5 x 29.5 |
150 mm |
105 mm |
40 |
11 - 14 |
6.5 |
16 |
note 79 |
g 2 |
14.4 x 19.5 |
23.0 x 29.0 |
145 mm |
100 mm |
40 |
11 - 14 |
6.5 |
16 |
note 80 |
g#2 |
13.7 x 10.2 |
22.0 x 28.2 |
138 mm |
94 mm |
40 |
11 - 14 |
6.5 |
16 |
note 81 |
a 2 |
13.4 x 18.5 |
21.0 x 26.3 |
134 mm |
90 mm |
40 |
11 - 14 |
6.8 / 7 buisje |
16 - changed to flat |
note 82 |
a#2 |
12.5 x 18.0 |
20.0 x 26.0 |
128 mm |
85 mm |
40 |
11 - 14 |
6.8 / 7 buisje |
16 - changed to flat |
note 83 |
b 2 |
12.2 x 17.3 |
20.0 x 25.0 |
122 mm |
80 mm |
40 |
9 - 10.5 |
5 / 5 buisje |
12 - changed to flat |
note 84 |
c 3 |
11.6 x 16.0 |
19.8 x 24.0 |
120 mm |
77 mm |
40 |
9 - 10.5 |
5 / 5 buisje |
12 - changed to flat |
note 85 |
c#3 |
11.6 x 16.0 |
19.0 x 23.6 |
114 mm |
72 mm |
40 |
9 - 10.5 |
5 / 5 buisje |
12 - changed to flat |
note 86 |
d 3 |
10.9 x 15.8 |
19.0 x 23.5 |
109 mm |
69 mm |
40 |
9 - 10.5 |
5 |
12 |
note 87 |
d#3 |
10.1 x 14.7 |
17.0 x 21.5 |
104 mm |
64 mm |
40 |
9 - 10.5 |
5 |
12 |
note 88 |
e 3 |
9.8 x 14.0 |
16.5 x 21.0 |
102 mm |
61 mm |
40 |
9 - 10.5 |
5 |
12 |
note 89 |
f 3 |
9.0 x 14.0 |
15.5 x 20.5 |
98 mm |
57 mm |
40 |
9 - 10.5 |
5 |
12 |
note 90 |
f#3 |
9.0 x 13.0 |
15.5 x 19.5 |
95 mm |
55 mm |
40 |
9 - 10.5 |
5 |
12 |
note 91 |
g 4 |
9.0 x 12.5 |
15.5 x 19.3 |
91 mm |
50 mm |
40 |
9 - 10.5 |
5 |
12 |
|
|
|
|
|
|
|
|
|
|
Size of the windchest upperplate in light oak-wood: 760mm x 240mm x 45mm. The
pipes are arranged in two rows, the first row holds the pipes 69 to 91 and the
back row the notes 55 to 68.
Approximate weight of the complete set of pipes: 20kg
Sizing of the wooden pipe-feet and pipes in two groups and/or rows on the windchest:
40 |
40 |
40 |
45 |
45 |
50 |
50 |
50 |
55 |
55 |
55 |
60 |
60 |
60 |
35 |
35 |
35 |
34 |
34 |
34 |
33 |
33 |
33 |
32 |
32 |
32 |
31 |
31 |
31 |
30 |
30 |
30 |
30 |
30 |
30 |
30 |
30 |
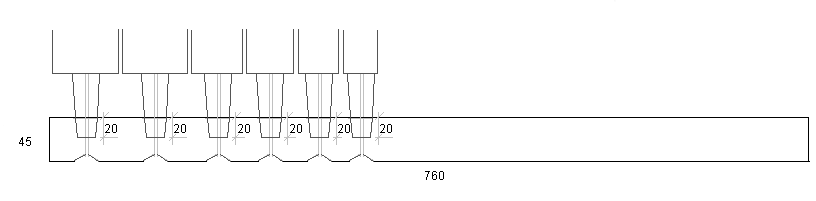
All pipes are switched by solenoid driven pallet valves with conical pads
25mm to 12mm in diameter. In order to make it possible to adjust the valves
in the windchest without having to remove all the pipes, we constructed the
pipeholder above the windchest such that it can be lifted up mechanically. Moreover,
even without lifting the pipeholder, the mechanical parts can be accessed through
the polycarbonate windows in the front and the back of the windchest. The electric
connection between valves and steering electronics makes use of a series of
Weidmueller connectors leaving the pipeholder through a vertical hole and a
windtight cable gland. A manometer can be mounted on the windchest to allow
for easy and precise adjustment of wind pressure in function of tuning operations.
A thermometer is mounted permanently inside the windchest.
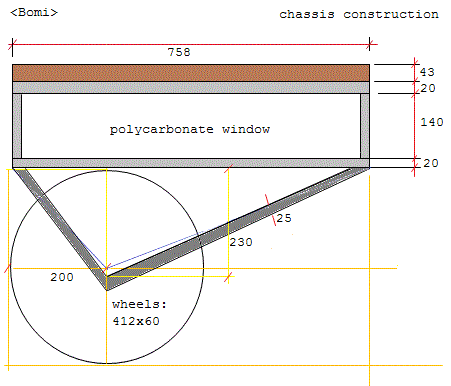
Preliminary view on the pipework assembled on the windchest during construction:
Circuit Overview:
- Hold velo boards: see <HarmO>
- Midi hub board
: see bottom of page
Mapping
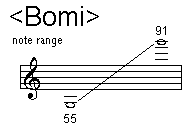
Midi implementation:
The midi channel for <Bomi> is 3 (0-15) or 4 (1-16).
Midi note range: 55 - 91. (c-g'') , velocity implemented (steers the speed
wherewith the valves do open en hence the note attack).
Individual note aftertouch (polyphonic) under development.
- note 120: front side white 30mm LED spotlight
- note 121,122,123,124: white lights inside windchest
- note 125: yellow 3W LED light under MidiHub board
- note 126-127: not yet mounted but implemented on the hub board
- note 0: Red 1W LED light under Midihub board.
Note Off commands are required.
Controller 66 is used to switch the motor on or off.
Controller 1 is used for the windvalve: at value 0 it is fully opened, at 127
it is fully closed. Thus by default and after reset the valve will always be
opened.
The tremulant is implemented as a modulation around the position of the windvalve
as set by controller 1. Default value for controller 1 when using the tremulant:
80. With high modulation depth (controller #12) it should be smaller.
Controller 11 controls the speed of the tremulant. Normal values are between
100 and 110. The tremulant speed is the midi value divided
by 10.
Modulation depth can be controlled with controller #12. Default value 60. This
is the excursion the valve will make around the central position as set by controller
1. More gentle effects are obtained by setting this controller to 38 (with CC11
to 100 and C1 to 90)
Note that tremulant speed, depth and windvalve position interfere with each other and not every combination of values will work well.
Controller 7 is used for the wind pressure (motor speed). The normal setting
should be 72. Default startup value in the PIC firmware is 0. It cannot be used
for fast wind pressure modulation but is perfectly suitable for slow crescendo
and decrescendo. Note however that the pitch as well as the intonation may be
affected when Bomi is operated on nonstandard wind-pressures.
<Bomi> responds to the midi all-notes-off command. This command also
switches off the lights and the wind valve, but not the motor. To switch off
the motor controller 66 should be used.
Technical specifications:
- size: 820 x 330 x 1230 mm. (w, d, h)
- weight: to be determined (portable, estimate: less than 50 kg)
- Note: this robot is not suitable for open air performances, unless it is
guaranteed to stay dry.!
- power: 230V ac - 286W(peak)
- Tuning: based on A = 440 Hz at 21 degrees Celsius
- static windpressure in the windchest for normal tuning and intonation: 45
mmH2O or 4.5 mbar
- Sound pressure level: max. ca. 84 dBA, motor background noise <= 42 dBA.
(Measured under normal operating conditions at 1 m distance)
- Ambitus: midi 55 to 91
- Insurance value: 19.000 Euro.
Design and construction: dr.Godfried-Willem
Raes (2009-2010)
Collaborators on the construction of this robot:
- Kristof Lauwers (2010)
- Yvan Vandersanden (2010)
- Johannes Taelman (2010)
- Xavier Verhelst (2010)
- Troy Rogers (2009-2010)
Music composed for <Bomi>:
- Bomi played the first time in public with the Logos M&M robot orchestra
on august 19th of 2010 in the Logos Tetrahedron.
- DEMO:
- A piece by Francois Couperin, adapted by Xavier Verhelst to Bomi, (Les Abeilles,
from 'Le Rossignol en Amour')
can be downloaded as MP3 file here. It demonstrates the expressive possibilities
of <Bomi> pretty well. If you want to see how it is coded in a midi
file, here
is a link to the midifile.
Nederlands:
Robot: <Bomi>
Voor de bouw van deze automaat maakten we gebruik van een eerder
toevallige aanbieding op de website van August Laukhuff, voor een volledig in
hout gebouwd 4-voet orgelregister met labiaalpijpen.
Dit
loopt vanaf midi noot 60 tot en met 91. De pijpen voor de noten 55-59 werden
speciaal bijgebouwd. De windlade is, afgezien van het bovenblad waarop de pijpen
rusten en waarvoor tropisch hardhout werd gebruikt, geheel vervaardigd uit gelast
inox en polykarbonaat, waardoor een transparante windlade kon worden gerealiseerd.
Geheel naar analogie trouwens met de windladen zoals we die eerder al ontwierpen
voor <Qt>, <Trump> en <Krum>. De elektromagnetische ventielen
waarmee de luchttoevoer naar de pijpen wordt geschakeld zijn ook hier binnenin
deze windlade geplaatst. In tegenstelling tot eerdere ontwerpen, gebruikten
we hier uitsluitend konische ventielen. Hierdoor wordt het mogelijk ook aftertouch
na het aanzetten van een noot te implementeren. Hiertoe wordt de houd-spanning
voor de elektromagneten in pulsbreedte gemoduleerd. Het elektronisch principeschema
moge dit verduidelijken:
Voor
de windvoorziening maakten we gebruik van een kleine Ventola orgelblazer van
de firma Laukhuff, met een regelbare winddruk van maximaal 80mm waterkolom,
of 8mBar = 785 Pa, in eenheden uit de fysika. De aansturing van de 80 Watt motor
gebeurt met een motorcontroller. Zoals voorspelbaar en normaal bij orgelpijpen,
is ook hier de stemming enigszins afhankelijk van de winddruk. Alleen bij een
motor AC frekwentie van 50Hz is de stemming korrekt. Winddruk 70mm H2O.
Om een eenvoudige afregeling, stemming en intonering mogelijk te maken, monteerden
we een precieze manometer aan de buitenkant van de windlade. Het maximale debiet
van de kompressor is 1 kubieke meter, wat dus brede klusters ruimschoots mogelijk
maakt.
De pijpen werden op de windlade gemonteerd in twee rijen overeenkomstig
de twee verschillende maten van de pijpvoeten. De elektrische verbinding tussen
de windlade en de elektronische besturing erbuiten gebeurt via een luchtdicht
afgesloten kabelbundel uitmondend op Weidmueller konnektors. De besturing van
<Bomi> komt voor rekening van niet minder dan 4 PIC mikrokontrollers:
drie voor elke groep van 14 pijpen en een voor de besturing van de motor, het
tremulant ventiel en de lichten. Alle elektronische besturingen, inklusief de
voedingen, vonden een plaatsje onder de windlade.
Aangezien het gehele pijpwerk uit hout is vervaardigd, is deze robot niet geschikt
voor openluchtkoncerten. Ze zijn niet in het minst vocht- of regenbestendig.
Bovendien is ook zijn eerder zachte toon, niet voldoende krachtig voor straatgebruik.
Als lid van het M&M robotorkest vormt hij evenwel een grote verrijking van
het orkestraal koloriet.
Tessituur:
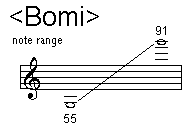
Audio-file demo: (Le
Rossignol en Amour, van Francois Couperin)
Midi-file
voor deze demo (file gemaakt door Xavier Verhelst).:
Building logbook / Bouwdagboek:
Omdat ons vaak wordt gevraagd hoeveel werk en tijd kruipt in,
en nodig is voor, het bouwen van dergelijke muzikale robotten, houden we ook
voor <Bomi> een beknopt en geilllustreerd bouwdagboek bij:
- 02.02.2009: eerste ideen en konkrete tekeningen, naar aanleiding van het
zien van de aanbieding op de Laukhuff website.
- 04.02.2009: Uitwerking van de mogelijkheid tot toepassing van konische ventielen,
waardoor hier velocity sensitivity evenals after touch zou kunnen worden geimplementeerd.
- 12.02.2009: bevestiging bestelling pijpwerk bij August Laukhuff.
- 13.02.2009: projekt prijskalkulatie uitgevoerd.
- 26.02.2009: Pijpwerk geleverd. Opmetingen mensuren.
- 27.02.2009: Eigenlijk zouden we beter nog 5 pijpen bijbouwen om de tessituur
naar onderen tot G uit te breiden. Dit zou het register ideaal geschikt maken
voor de orkestratie van zachte vioolpartijen...
- 28.02.2009: Pijpen voor 55-59 bijbesteld bij Laukhuff...
- 02.03.2009: Zoektocht naar een geschikte 50mm dikke plank voor de konstruktie
van het bovenblad van de windlade. Een harde gladde kunststof ware natuurlijk
een nog betere keuze...
- 03.03.2009: Om de konische gaten in de windlade te boren hebben we boren
nodig met een snijhoek van 105 graden.
- 04.03.2009: De extra pijpen gaan ons zo'n 350 Euro kosten. Wel moeten we
eerste de twee laagste opsturen om de kwa mensuur en opsnede te laten aansluiten.
- 05.03.2009: Ontwerpberekeningen wijzen uit dat vertikaal werkende trekmagneten
met een sterke veer eigenlijk ideaal zouden zijn voor de bediening van de
konische ventielen. Dit zou de windlade ook heel wat kleiner kunnen maken.
- 06.03.2009: Afmetingen windlade berekend en vastgelegd.
- 07.03.2009: Overall sketches for the design.
- 28.03.2009: Still waiting for the five missing pipes as well as for the
ordered wood for the upperplate of the windchest.
- 30.03.2009: e-mail enquiry to Laukhuff in order to get a shipment date.
- 06.04.2009: Wood plate for the windchest delivered. There are some deficiencies
in the grain structure however. Lets hope we can work around it.
- 07.04.2009: Start tentative positioning of the pipes on the windchest. The
5 missing pipes came in!
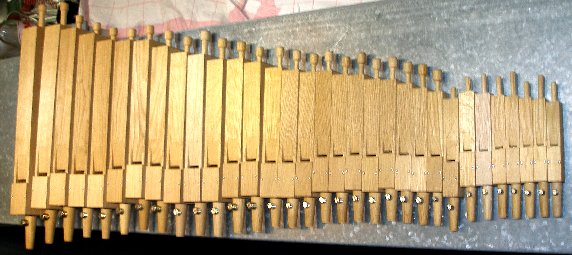
- 26.04.2009: Bomi implemented in our GMT driver software.
- 15.05.2009: Search for usefull milling tools to make the windchest cones
as well as holes for the pipe feet.
- 22.05.2009: First sketch for positioning pipes on the windchest.
- 29.10.2009: solenoids for the valves ordered from Laukhuff.
- 04.11.2009: Solenoids delivered from Laukhuff.
- 05.11.2009: construction of a prototype conical valve with a seating in
hard wood. This prototype can be used as a tremulant on <harmO>.
- 15.11.2009: The conical valve prototype works very well but not at all for
the function we wanted it to use for: a tremulant...
- 21.12.2009: Spoke wheels ordered from Kaiser+Kraft (412 x 60, with massive
polyurethane tires).
- 23.12.2009: drilling of the upper plate of the windchest. Milling of the
pipe-holding holes. First tentative placement of the pipes:
The pipes will need some form of protection on their tops, since touching
of the pipe stoppers detunes them and chances that people will touch them
are pretty realistic.
- 24.12.2009: Further design of the windchest, with provisions for a moving
coil tremulant. Calculation of the power supply requirements.
- 25.12.2009: Drawing of the windchest construction and start cutting stainless
steel profiles.
Welding works on the frame of the windchest. 40 holes drilled (4.2 mm holes)
and tapped with a M5 thread to hold the polycarbonate plates.
Cutting
of the side plates from 3 mm thick stainless steel. The bottom plate will
have to be made of 2 mm thick material, since we do not have enough 3 mm plate
in stock... 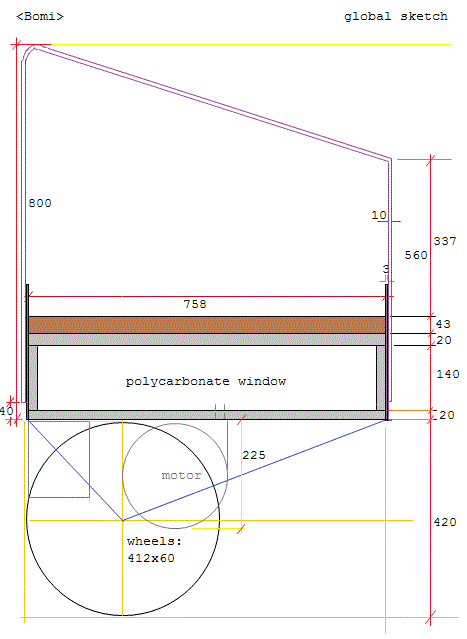
- 26.12.2009: Bending of the staves to protect the pipes from being touched
and detuned. Stainless steel bar 30x10. These structures have four10 mm holes
to fix them to the sides of the windchest. Polishing of these staves. Cutting
of the underplate of the windchest 240 mm x 760 mm, 2 mm thick fine grain
stainless steel.
- 27.12.2009:
Left side plate drilled and welded to the windchest chassis.
The protective bars are to be mounted with M10 hex inbus bolts. Design of
the trolley. Drilling of the right side plate. The 20mm diameter holes are
merely decorative.
- 28.12.2009: Welding of the right side plate on the chassis. Study of the
motor mounting problems and the approaches possible to make a fast moving
wind slide. Meeting with Johannes Taelman conscerning the implications on
the firmware level for the PIC controllers. Start welding and cutting of the
wheel base. Here we use square stainless steel pipe 25x25x2.
- 29.12.2009: Further welding work on the wheelbase. Construction of the mounting
bracket for the motor controller. Positioning of all the components: boards
and power supplies. First calculation of the conical valve required for the
implementation of fast wind controll and flow tremulant by Troy Rogers:
If we build this, the solenoid has to be open at rest, since by default (and
most of the time in normal use) this valve will be opened at full.
- 30.12.2009: Precise determination of the center of the wind inlet hole,
diameter 32 mm. Drilling of this hole as well as of the hole required for
the windtight cable gland for the electric connections of the solenoids, 12
V power supply, 24 V power supply, transformers, and other components that
need to be mounted against the underside of the windchest. All drilling should
be done before welding the chassis together. Cutting and drilling of a mounting
plate for the mains switch and a 30 mm LED spotlight, placed on the front
side. The power entry (3-prong europlug) as well as the Midi-input and thru
connectors will go on the other side. The mounting plate for the power entry
was cut from a piece of stainless steel 30x30x3 profile, 150 mm in lenght.
The pulse/hold boards will mount on a polycarbonate plate fixed to the 25x25
profiles. Board protection will be provided by the wheels.
- 31.12.2009: Further work on the base plate of the windchest. Final welding
of the wheel base to the upperpart of the windchest.
Reaching the end of the year, we seem to be reaching the end of our bottle
of argon gas as well... Design of the internal lights. First assembly test:
- 01.01.2010: Mounting of the 12 V power supply, a Power-One part number HN12-5.1
analog module, under the windchest. Mounting of the Siemens motor controller
and wiring of the motor. Mounting of the small 24 V SMPS power module and
the transformer for the 5 V power supply. Mounting of the four white LED assemblies
inside the windchest as well as of the external white LED spot. Wiring of
the power switch. Windchest sealed with Parabond.
- 02.01.2010: Cutting of polycarbonate window plates as well as a carrier
plate for the note-velo driver boards and the midi-hub board. Workshop clean-up...
many visitors tomorrow.
- 04.01.2010: Further calculations on the conical valves.
- 07.01.2010: Start assembly of the conical pallets on the solenoid valves
for the pipes. The pads are mounted with M2x20 bolts and nuts. All helical
springs replaced with H25 E4.5 D0.5 custom made steel springs. Valve cones
-missing sizes- ordered from August Laukhuff. (Catalog numbers 409105, 409106
and 409107).
- 15.01.2010: The ordered conical valve cones have flown in... Now trying
to trace suitable milling devices.
- 16.01.2010: We decided to make the required mills ourselves starting from
old and worn out large size HSS drills. Construction and assembly of the conical
solenoid valves, nine diameter 12 mm, cone angle 72°, 10 diameter 16 mm,
cone angle 81°, 10 diameter 18 mm, cone angle 85°, 8 diameter 24 mm,
cone angle 100°.
The cones are fixed to the solenoid assembly with M2 stainless steel bolts
and nuts. For the smallest cones M2 x 10 was used, whereas for the others
it became M2 x 20 (we didn't have M2 x 16 in stock...).
- 17.01.2010: our self-made mills (seen on the picture above) appear not to
be precize enough: the valve seats do leak on our test boards. Thus we decided
to enquire for custom made mills at Lanoye bvba. The specs are as follows:
The requested sizes for the five required mills are:
mill nr |
d1 |
d2 |
cutting angle
a
|
2 |
0 - 15mm |
35 mm |
110° |
4 |
0 - 9mm |
25 mm |
100° |
5 |
0 - 8mm |
20 mm |
85° |
6 |
0 - 6mm |
16.5 mm |
81° |
7 |
0 - 5mm |
13 mm |
72° |
Mills with at least four cutting faces seem to be required.
- 18.01.2010: Further assembly and soldering works on the velo/hold boards.
All boards soldered. No parts missing. The boards are ready for being programmed
now. On the two lowest note boards, we mounted BSP254A
P-channel mosfets, whereas on the highest note board we used BS250 types.
It shouldn't make a difference. All power mosfets mounted are IRL640. The
five highest outputs of the high note board are wired a bit differently: these
outputs are used to steer the lights.
The ground and power supply bars can be seen on the picture below:
The valve solenoids having a resistance of 80 Ohms, draw each 150 mA on hold.
For full polyphony, this entails a power supply with a capacity of at least
5.6 A. As to the power supply calculation for the velocity voltage: if we
take this one at -24 V then the voltage over the solenoids for the duration
of the pulse will be 36 V. The current being 450 mA. If now we can obtain
our velocity range with pulse durations no longer than 12 ms -minimum time
between any two midi commands being 1 ms- then the worst case current becomes
5.4 A. No news as yet from our mill-maker...
- 19.01.2010: Construction of the mounting bracket for the pulse/hold board
assembly. We will not have a price offer for our mills before the end of the
week...
- 20.01.2010: The ordered spoke wheels can be expected by the end of the week.
Design of the carying structure for the midi-hub and motor control board.
- 25.01.2010: The spoke wheels came in. The axis are 12 mm diameter. Stainless
steel axis cut, length 320 mm. No news as yet from the mills.
- 27.01.2010: Just got a quote for the mills. A set of five would cost ca.
1500 Euro. Worse than that: delivery time will be four weeks... Will have
to negociate...
- 30.01.2010:Work on the math for the calculation of the conical valves:
Calculated results for Bomi:
-
cone diameter |
top angle |
traject |
diameter of equivalent orifice |
35 mm / 15 mm |
110° |
5.2 mm |
10 mm |
25 mm / 12 mm |
100° |
5.0 mm |
7 mm |
20 mm / 11 mm |
85° |
6.0 mm |
5 mm |
16.5 mm /10.2 mm |
81° |
6.0 mm |
4.3 mm |
13 mm/ 8.7 mm |
72° |
6.0 mm |
3 mm |
The diameter of equivalent round orifice should be taken such as to correspond
with the diameter on the inlet of the organ pipes used. By increasing the
traject a bit, adjustments to the exact sizings of the pipe feet are possible.
For Laukhuff pallet valves, the traject should be kept smaller than 10 mm.
If we take the traject too small, -say smaller than 4 mm- , resolution of
the regulation possibilities will suffer. We added a calculation utility
to our g_indep.dll library in GMT to facilitate generation of lookup tables.
The relevant exported function is prototyped as: FUNCTION FrustumFlow (BYVAL
traject AS SINGLE, BYVAL diam AS SINGLE, BYVAL angle AS SINGLE) AS SINGLE.
It returns the diameter of the equivalent circular orifice. The source code
to be compiled with the PowerBasic CC compiler
is here. The compiled program here.
The resulting lookups here.
- 01-03.02.2010: further work on a generalized design software for conical
valves. Some bugs discovered in our first version of the implemented math.
For cones with a top angle of 90 degrees, the traject will allways equal the
orifice. An easy rule to keep in mind.
- 03.02.2010: Visit to the mill-maker, Lanoye with Troy Rogers and Sebastian
Bradt. The mills could be ready by next friday...
- 04.02.2010: To facilitate comparative calculations we also worked out the
math for flat valves:
The results prove the superiority of conical valves but also make clear that
for trajects in the order of 4 to 8 mm, the use of conical valves on very
large orifices would not be appropriate. For instance, it would not have been
a good choice on the lowest pipes of our <Qt> robot.
- 05.02.2010: Expecting mills to flow in...
- 13.02.2010: Still no mills...
- 20.02.2010: Mills anounced for tuesday 23th...
- 22.02.2010: Mills tomorrow?
- 23.02.2010: Indeed, we just got the mills required to finish the upperplate
of the windchest.
- 03.03.2010: Work on the tremulant valve continued. If we use a spherical
valve here, it ought to have a diameter of 60 mm.
- 04.03.2010: welding works on the tremulant subchassis. Now we extended the
anchor with a 1/4" brass rod, threaded with M6. After cutting a thread
inside a conical 35 mm diameter valve we obtain a fully adjustable valve.
- 09.03.2010: The tremulant valve now looks like this:
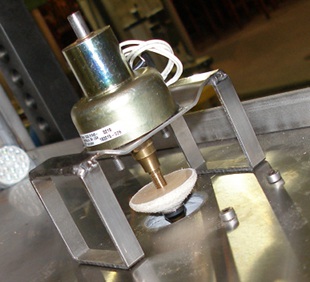
- 23.05.2010: Work on Bomi taken up again... Design of the holder for the
midi hub board.
- 25.05.2010: Start constructing of the standing leg. We will make this removable
to ease access to the electronics later on. The connection with the chassis
is through two M10 x 50 mm bolts. The flat floor plate has a glued on hard
rubber face.
- 26.05.2010: Standing leg finished and mounted in place.
- 27.05.2010: Wheel ball bearings mounted. Will we need to provide a steering
handle?
- 10.06.2010: Drilling and mounting of the holding structure for the midi
hub board. Wiring of the mains power lines, the power inlet and the main power
switch.
- 13-14.06.2010: Milling works on the conical valve seats in the windchest.
Adjustments on the holes for the pipe feet.
- 15.06.2010: Start mounting of the pipevalves on the windchest.
All valves mounted,
airtightness check and adjustments still to be done. One valve seat (note
56) needs a repair, where our mill slipped out.
- 16.06.2010: First correction round for airtightness of the valves. We assume
about five rounds may be required to get it all done to perfection. Recalculating
the time schedule, Bomi can be expected to join the orchestra in july or august
at the latest... if nothing fundamental goes wrong.
- 03.07.2010: Wiring windchest with rainbow colored wires. Wiring tables adapted
accordingly. The common positive power wires use the pink colored wires.
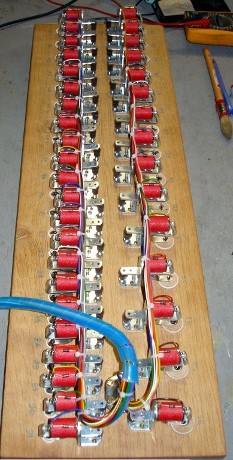
- 04.07.2010: Through hole drilled in windchest for the tremulant valve and
the lights. Sealed with a highly liquid silicone kit (Loctite 596, red). Wiring
of lights inside the windchest finished. Holes drilled for fixing the pipeholder
plate on the windchest. Tremulant valve mounted using silicone kit exclusively.
Hopefully it will hold...
- 05.07.2010: Cutting of the polycarbonate windows for the front and backside
of the windchest. Drilling of all mounting holes (5.5 mm) for all 40 M5 bolts.
The way the pipeholder plate is fixed to the windchest had to be revised.
Countersunk bolts are impossible since the polycarbonate leaves us too little
space. It will be better to thread the holes with M5 threads and use M5 x
50 bolts going through the upperplate.
- 06.07.2010: Threads made in holding profiles for the pipe carrier plate.
Holes drilled to allow for 6 M5x50 bolts, sticking out as little as possible
through the profiles. Routing of the cable bundle from the solenoids to the
controller boards. Wiring finished of the white LED lights inside the windchest.
The tremulant valve will have to be connected to the midi hub board and thus
still has to wait.
- 07.07.2010: Sealing of the cable bundle leaving the windchest: Loctite Red.
Start wiring of the solenoid connectors. Wiring of the frontal light.
- 08.07.2010: Windchest wiring finished. Wiring of the power supplies.
- 09.07.2010: Midihub board redesigned. Waiting for firmware.
- 10.07.2010: Wiring and component placement of midihub board. Motor controller
wiring finalized. Circuit drawings updated.
- 11.07.2010: Wiring of the tremulant softshift solenoid. Revision of the
midi implementation to be coded in the firmware.
- 12.07.2010: Mounting of midihub board finished. First electrical test. All
power supplies are o.k. and we do not seem to have any shorts. However, the
red copper powerrails under the pulse/hold board need washers as they cannot
be tightened for enough pressure to guarantee optimum electrical contact.
- 13.07.2070: Weather stripping (Tesa, 10 mm wide soft rubber) applied to
upperside of the stainless steel profiles to seal the openings between the
wooden pipeholder and the windchest chassis. Thickness of these strips is
about 2.5 mm.
- 16.07.2010: Finishing back windchest polycarbonate window. The upper left
above corner is marked.
- 18.07.2010: Meeting with Johannes Taelman on the Bomi PIC firmware.
- 23.07.2010: Taking up the work on Bomi again...
- 24-25.07.2010: test code for hardware and firmware debug of Bomi written
in GMT.
- 06.08.2010: Pipes mounted on the windchest using Teflon tape.
- 07.08.2010: First version of PIC firmware programming session with Johannes
Taelman. Came out we forgot to solder the pull up resistor on pin1 on the
PIC of the hub board (18F2525)... First version of the firmware runs fine.
Default start-up value for the motor controller (cc7) is now 100. CC1 is 0
at startup: valve inactivated and fully opened. Next thing to do: leak reduction,
tuning session and silencing of the motor... Bug report after testing: ctrl
66 is shaky. Note 76 is coupled to note 84, the inverse is not true... CC1,
windvalve works fine. Motor speed CC7 works fine as well. As to the valve
mechanics: we seem to have only a few leaks on the highest pipes.
- 08.08.2010: Weather stripping applied to the frontal window of the windchest.
First rough tuning and intonation. Periodic tremulant implemented in GMT.
This works nicely, but learns us that for a PIC firmware implementation, we
need two controllers: CC11 for the periodicity (speed) and CC12 for the modulation
depth. Documentation updated.
Bug in PIC velo/hold board remedied by Johannes Taelman. Complete first tuning
of all pipes on 47 Hz motor frequency. Bomi played its very first musical
piece: an invention by Bach. This is a picture of <Bomi> taken from
its backside:
First session for closing the leaks on 85, 96, 90, 72, 64, 65... This is always
a very tedious undertaking. Result: still leaks on 90, 71, 72, 66. The other
ones are cured.
- 09.08.2010: Motor wires swapped such that the direction of rotation is correct
without the resistor on the cw/ccw input of the motor controller. Considering
to add a manual motor controller reset one-shot switch. This would be handy
on other robots as well! First demonstration for the people and collaborators
at Logos: Sebastian Bradt and Kristof Lauwers.
Second tuning session performed under windpressure of 4.3 mbar (43 mm H20)
measured in the windchest, corresponding to a motor frequency of 42 Hz and
a midi controller 7 value of 50. When this controller is set to 60, the pitch
goes up ca. 20 cents. With the controller set to 40, it goes down almost a
quartertone. We prefer performing tuning and intonation on the lowest possible
wind pressure in order to minimize motor generated noise. Unfortunately the
Laukhuff motor tends to be pretty noisy.
First experimental design of a handle, using an M20 stainless steel bolt.
Second run through closing leaky valves: note 72 remains stubborn and leaky...
- 10.08.2010: Thirth run through closing leaky valves. Only pipe 72 still
has a very small leak now. After consulting with Xavier Verhelst we decided
to settle the standard windpressure to 60 (cc7 setting) corresponding to a
wind pressure of 4.5 mBar, New tuning session and run through all pipes: wind
pressure 4.5 mbar (midi CC7 setting 60, motor frequency 47.2 Hz. Environment
temperature: 22 degrees Celsius.
<Bomi> signed in front with a brass name plate... We are very pleased
with the results of the softshift tremulant and its control possibilities.
This design can definitly be replicated in following organ like robots.
- 11.08.2010: Large size washers added to all M5 bolts for closing the windchest
transparant panels. Fixing the pipes on the windchest with Teflon tape is
a quite perfect solution, but will it be resistant enough when transporting
the robot in a truck? Wouldn't wax or even hotglue be a better solution?
Start experimental construction of a silencer. Motor noise, after filling
all gaps, measured 1 m from the front side is 48 dBA, from the back only 42
dBA. Thus, by rerouting the wind inlet for the motor to the backside we could
win maximum 6 dBA in noise reduction. Whilst we were at it, we also measured
the maximum sound pressure level for Bomi with about 18 pipes playing: 84
dBA. When more pipes are speaking, sound pressure level does not really rise,
since that makes the wind pressure collapse. This result conforms our design
in that we were after a rather soft and gentle sounding organ.
- 12.08.2010: Small leak on note 87... Further experiments with motor silencers.
- 13.08.2010: PIC programming session for tremulant and aftertouch postponed...
- 14.08.2010: Silencer mounted on motor inlet using Parabond 600 kit.
- 15.08.2010: some leaks seem to reappear. Pipe intonation for note 90 adjusted.
It was speaking softer than the others.
- 16.08.2010: To make adjusting of the pallets easier we designed and made
two special tools.
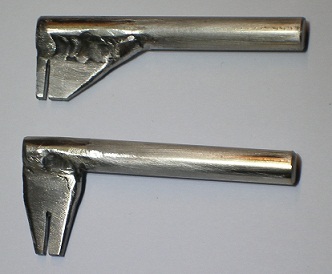
- 17.08.2010: Windchest opened again. Thermometer mounted inside against the
wall. All pallet valves regulated for minimum clicking noise and optimum trajectory
of movement. Leaks on pads 55, 62, 69, 71, 72, 74, 76, 80, 81, 84, 90, 91
remedied. After closing de windchest again: still leaks on pads 81, 72 and
90. The leaks on 72 and 90 disappeared after some scale playing. The 81 leak
seems persistent, although very small. Loudness of pipe 90 corrected. Pipe
72 still speaks softer than the others.
- 18.08.2010: Finalising. All day rehearsals for the ancient music concert
tomorrow. Noticed an issue with Bomi: we performed tuning and intonation after
a warm-up time, thus with the windpressure present in the windchest. Temperature
rise inside the windchest is ca. 6°C. If the instrument is 'cold' (ambient
temperature) than when it is switched on and plays, the tuning will be a bit
off (lower than normal). Applying a very small overpressure at startup and
letting this go back to normal over a timespan of 5 minutes is a possible
remedy. An alternative consists of never reducing the windpressure to values
lower than midi cc7= 30, thus guaranteeing a minimal temperature difference.
It is clearly impossible to tune the instrument with great precission and
cold, for the time required to do the tuning takes much longer than the warm-up
time.
- 19.08.2010: An ultimate tuning round. Bomi plays its first public concert...
and did it very well!
- 20.08.2010: Redesign of the steering handle. Market check to find a small
barometer with a range op to 1100 mbar to place inside the windchest.
- 09-10.10.2010: <Bomi> plays on the opening of the STAM museum on the
Bijloke campus: 12700 visitors...
- 14.10.2010: Pipe 72 has a leaking valve and needs adjustment. Also we noticed
some anomalies in the motor control (midihub firmware). Power on always starts
the motor on its highest speed.... We start rewriting the firmware in the
Proton+ compiler under MPLAB.
- 15.10.2010: Debug and testing of the new firmware (Version 2.0) for the
hub board. The tremulant works very well now. Lites mapped on note 0 and 125
added in the hardware and implemented in the firmware with note pressure for
automated flashing.
- 17.10. 2010: Motor CC7 to pressure and frequency table updated with new
measurement data. We still settle the standard windpressure the new 72 cc7
setting, corresponding to a wind pressure of 4.5 mBar and a motor frequency
of 47Hz. Environment temperature: 22 degrees Celsius. GMT declared constant
values adapted.
- 02.12.2010: Small leak on note 72 reappeared...
- 12.02.2011: Scientific paper on Bomi finished. This is to be published by
ARIP. The PDF can be downloaded here.
- 15.02.2011: The valve seating of the tremulant has moved a bit downwards
and needs readjustment. We did the adjustment and secured the wooden thread
with a drip of cyanacrylate glue.
- 16.02.2011: demo recording made of
Francois Couperin, Les Abeilles (from Le Rossignol en Amour) and made available
for mp3 download.
- 09.03.2011: Construction of a pipe support rail for the low pipes, such
that they stay better in place and keep tuning during transportation. The
rail can be removed by loosening the two M4 inbus bolts at the ends.
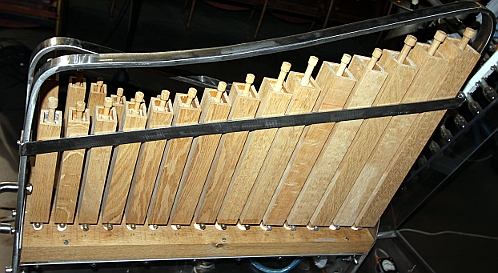
- 18.03.2011: Bomi presented on the ARIP day organised by the Music Department
of the Ghent University Association. Publication of our paper on design and
construction of the Bomi robot.
- 10.05.2011: Leak on note 72 came back. It's persistent...
- 28.05.2011: New firmware written for the midi-hub board. Lite and tremulant
implementation improved.
- 29.05.2011: Bug killed in hub firmware. Now tested and found o.k. Worksession
on closing the valve leak on note 72. Even after sanding the conical hole,
the leak seems very persistent.
- 30-31.05.2011: We left valve 72 switching on/off for 48 hours at a rate
of 5 notes a second. See whether this cures the disease.
- 01.06-05.2011: Leak seems cured now.
- 07.06.2011: All of the sudden more than 7 leaks... what happened to Bomi???
Note 75 persists now...
- 08.06.2011: Further checks after a night long warm-up, slight alignment
of valves and treatment with some talc.
- 20.08.2011: Leak on note 75 cured. Tuning session for all pipes. Some need
reintonation.
- 21.08.2011: Pipework tuning checked and corrections performed where needed.
Leak did not re-appear sofar...
- 12.01.2012: Leak on note 79, caused by fast tremolo with very low wind pressure.
Users should also be warned that having wind pressure on maximum without having
any notes playing, is an open solicitation to audible leaks.
- 20.03.2013: Construction of protection materials to facilitate transportation.
The pipes ought to be protected against movement.
The pictures show the
construction of the holder for the backpipes with foam, clamped for glueing
between two pieces of wood. The last two pictures show the way the pipe protectors
should be mounted on the robot.
- 20.04.2013: <Bomi> survived the trip to Glasgow very well! We expect
her back in Ghent on monday 22nd of april.
- 13.04.2015: Persistent leak on note 72. Repair required.
- 24.04.2015: A thorough check of Bomi revealed quite some deficiencies: Notes
57, 61, 73, 83 do not speak properly. Note 69 solenoid rattles a bit, note
84 doesn't repeat well and the valve trajectory for note 74 is too small.
The leak on 72 is persistent. Opening the windchest and getting everything
realligned is needed.
- 25.04.2015: Apparently, when checking again after a cold boot, everything
(apart from the note 72 leak) worked well again... The velocity control mechanism
in the PIC firmware clearly failed. As no velocity pulses were generated,
clearly some pipes did not get to speak at all. There must be an overflow
condition somewhere in that part of the coding. Windchest opened in an attempt
to cure the leak on pipe 72. As we suspect the solenoid assembly was mounted
too loosely on the wood of the windchest, we applied some clear silicone on
the mounting plate to keep it in place.
- 28.10.2016: <Bomi> on the road to Brugge for 'Iedereen Klassiek'.
- 30.10.2016: <Bomi> set up again in the orchestra and found fully o.k.
Some tuning is required though.
- 06.01.2018: Quick run through the tuning, Corrections applied where needed.
Some pads need readjustment but to do this we have to disassemble the entire
windchest.
- 14.02.2018: Tuning session in <Bomi>. Bomi suffers a lot from varying
humidity and temperature, a result from budget cuts and loss of structural
subsidy.
- 12.03.2018: Windchest opened for readjustment of some valves. Valve 72 remains
stubborn. Notes 83 and 84 have a small leak.
- 13.03.2018: After a full day of work, we made things go only worse... pipes
83,84,85 are leaking now. Pipe 72 seems cured for the time being... Could
the return springs have lost power?
- 15.03.2018: Valves for pipes 83,84,85 changed with a piece of 5 mm brass
pipe and a flat valve. Valves for pipes 81, 82 changed: bore hole drilled
to 6.8 mm and brass tube 7 mm inserted. Flat valve mounted onn the rim of
the brass tube. This now is leak free, but the pipes do not seem to get enough
wind now. Full working day... To be done: 84 still leaking after 2 hours of
playing. Insert larger brass pipes on the notes that do not get enough wind
now.
- 17.03.2018: Backrow pipes now fixed to the pipe holder bar using strips
of self adhesive velcro. Pallet trajectory for note 81,82 enlarged. Still
these pipes are in need of more wind. We will have to enlarge the diameter
of the inlet pipes. No more leaks now... Wait and see, read hear. Maybe we
should consider adding a pipe holding bar also for the front row pipes, using
velcro.
- 22.09.2018: <Bomi> left off to Manchester for a Heiner Goebbels production
and 10 concerts.
- 23.10.2018: <Bomi> returned from Manchester. Tuning session.
- 30.11.2018: Motor wiring and specs completed.
- 02.02.2021: Bug discovered in the hardware of the note-velo drivers: the
gate voltage exceeds +20V during the velo pulse. We should add a zener diode
across the 4k7 gate resistor, as shown in this corrected circuit drawing:
Any
zener diode with a zener voltage between 5V and 20V will do here.
- 27.09.2021: On return from the exhibition from SMAK, a few pipes/notes found
to be leaky: 71,80,89,91. We have to check the cone-valves. <Bomi> has
been playing for 25 days without interruption...
- 31.01.2022: Herstelwerk door Mattias Parent en Philippe Druez: De conische
ventielen van midinoten 66, 69, 75, 78,79 en 80 zijn vervangen door platte
kleppen. Het lekvrij maken bleek (alweer) problematisch.
- 18.09.2023: <Bomi> is aangekomen in Berlijn. Er was een draadje los
aan de motorcontroller, maar dat was wellicht intentioneel en ook al zo bij
vertrek.
- 27-28-29.09.2023: <Bomi> plays in the Zeroth Law production for the
Deutsche Oper Berlin. 1 wat onbetrouwbaar werkend ventiel (noot 77) verholpen
door de pijp stil te maken... Moet in de werkplaats in Gent verder onderzocht
worden.
- 13.11.2023: Nazicht en grondige stembeurt. Probleem met ventiel voor noot
79: doet helemaal niets... Verder te onderzoeken.
To be done:
- Finishing of the programming for the firmware in the PIC controllers for
the velo/hold boards, with aftertouch control.
- Sysex programming for velo-scalings.
- Construction of a definitive steering handle.
- Adding another spooky sound underneeth the windchest.
- Adding a heater resistor inside the windchest and a temperature controller
to keep temperature inside at a constant 28°C
- Construction of a complete transportation case.
Robodies Pictures with <Bomi>:
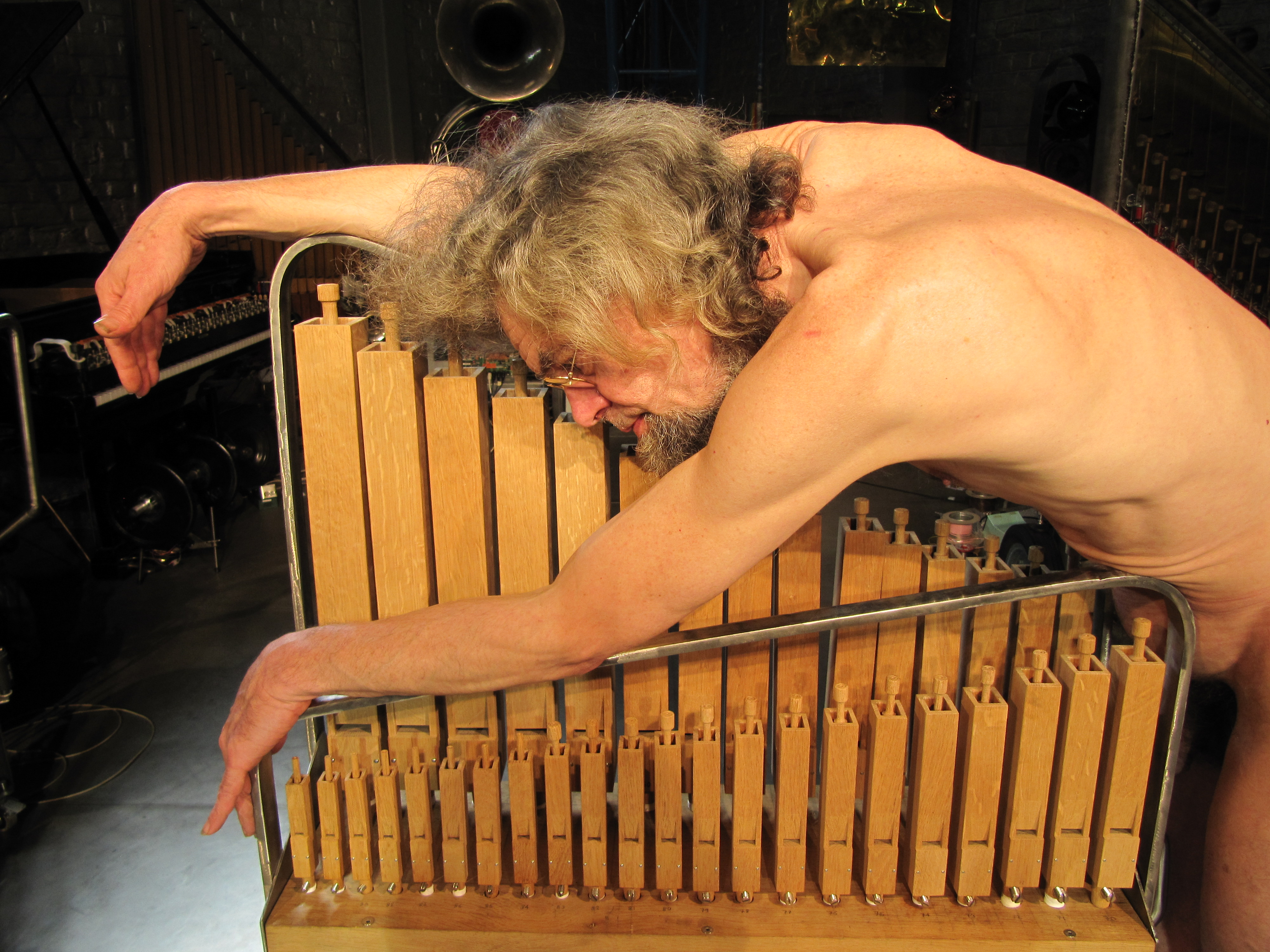
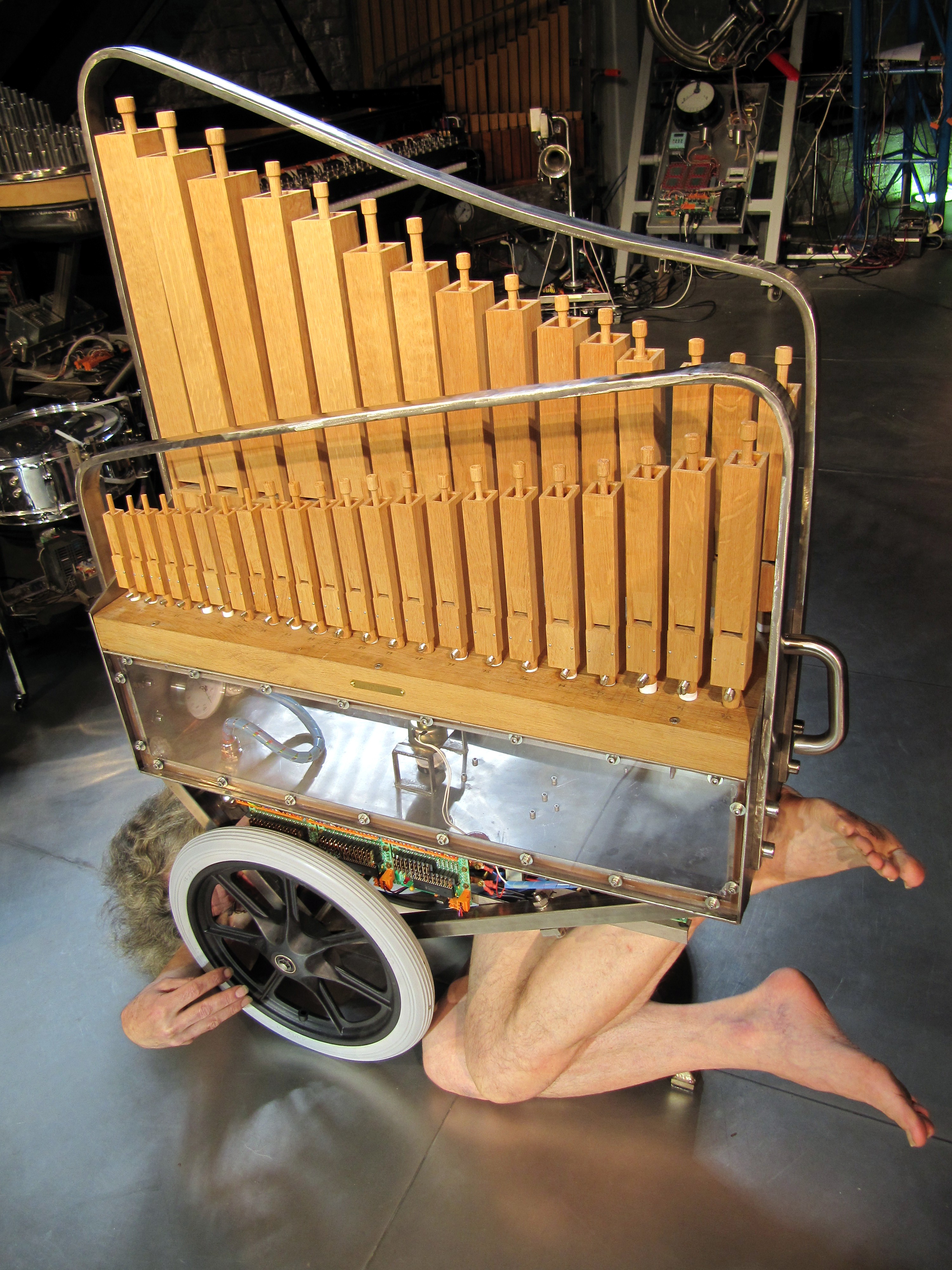
Last update: 2025-07-14
by Godfried-Willem Raes
Technical data sheet and maintenance instructions:
- Motor specs: Laukhuff Mini Ventola. Order number 612150. Motor noise level
under normal operational conditions: ca. 45 dBA. Rewired for 3-phase triangle
operation:
- Motor Controller: Siemens Sinamics G110
- PIC controllers: 1 x Microchip 18F2525, 3 x 18F4625 firmware coded in assembler
by Johannes Taelman
- Power supply:
- Hold voltage: 12 V/ 5.1 A supply, Power-One part nr. HN12-5.1-AG, Farnell
order number: 120-8823
- Velo pulse voltage: 24 V SMPS module, 2.5 A
- Logic 5 V supply: from separate transformer. Rectifier and stabilising
parts on the midihub board.
- Front light: LED spot, 30 mm, 12 V. (warm white)
- Lights inside the windchest: 12 V/110 mA LED white spotlites, disassembled
from 50 mm diameter bulbs.
- Optional manometer: 0-10 mbar (now this is an external accessory)
- Thermometer inside the windchest: important for determination of the tuning
conditions, since we noticed the compressor heats the wind in the windchest
noticably. (28 degrees Celsius).
- Motor Wiring detail: triangle connected, 3x132 V - 0-75 Hz, 70 W, 2800 rpm
at 50 Hz
Wiring tables for the three PIC 18F4625 controller boards:
Board 1:
board output |
connector pin |
mapping |
wire color |
remarks |
PIC pin |
1 |
2 |
note 55 |
black |
pulse/hold |
4,3 |
2 |
3 |
note 56 |
brown |
pulse/hold |
2,5 |
3 |
4 |
note 57 |
red |
pulse/hold |
6,7 |
4 |
5 |
note 58 |
orange |
pulse/hold |
8,9 |
5 |
7 |
note 59
|
yellow |
pulse/hold |
10, 37 |
6 |
8 |
note 60
|
green |
pulse/hold |
36, 35 |
7 |
9 |
note 61 |
blue |
pulse/hold |
34, 33 |
8 |
10 |
note 62 |
purple |
pulse/hold |
30, 29 |
9 |
12 |
note 63 |
grey |
pulse/hold |
28, 27 |
10 |
13 |
note 64 |
white |
pulse/hold |
24, 23 |
11 |
14 |
note 65 |
black |
pulse/hold |
22, 21 |
12 |
15 |
note 66 |
brown |
pulse/hold |
15, 16 |
13 |
17 |
note 67 |
red |
pulse/hold |
17, 18 |
14 |
18 |
note 68 |
orange |
pulse/hold |
19, 20 |
Board 2:
board output |
connector pin |
mapping |
wire color |
remarks |
PIC pins |
1 |
2 |
note 69 |
yellow |
hold/velo |
4, 3 |
2 |
3 |
note 70 |
green |
|
2, 5 |
3 |
4 |
note 71 |
blue |
|
6, 7 |
4 |
5 |
note 72 |
purple |
|
8, 9 |
5 |
7 |
note 73 |
grey |
|
10, 37 |
6 |
8 |
note 74 |
white |
|
36, 35 |
7 |
9 |
note 75 |
black |
|
34, 33 |
8 |
10 |
note 76 |
brown |
|
30, 29 |
9 |
12 |
note 77 |
red |
|
28, 27 |
10 |
13 |
note 78 |
orange |
|
24, 23 |
11 |
14 |
note 79 |
yellow |
|
22, 21 |
12 |
15 |
note 80 |
green |
|
15, 16 |
13 |
17 |
note 81 |
blue |
|
17, 18 |
14 |
18 |
note 82 |
purple |
|
19, 20 |
Board 3:
board output |
connector pin |
mapping |
wire color |
remarks |
PIC pins |
1 |
2 |
note 83 |
grey |
pulse/hold |
4, 3 |
2 |
3 |
note 84 |
white |
pulse/hold |
2, 5 |
3 |
4 |
note 85 |
black |
pulse/hold |
6, 7 |
4 |
5 |
note 86 |
brown |
pulse/hold |
8, 9 |
5 |
7 |
note 87 |
red |
pulse/hold |
10, 37 |
6 |
8 |
note 88 |
orange |
pulse/hold |
36, 35 |
7 |
9 |
note 89 |
yellow |
pulse/hold |
34, 33 |
8 |
10 |
note 90 |
green |
pulse/hold |
30, 29 |
9 |
12 |
note 91 |
blue |
pulse/hold |
28, 27 |
10 |
13 |
light note 120 |
grey |
hold (front) |
24, 23 |
11 |
14 |
light note 121 |
green |
hold |
22, 21 |
12 |
15 |
light note 122 |
purple |
hold |
15, 16 |
13 |
17 |
light note 123 |
yellow |
hold |
17, 18 |
14 |
18 |
light note 124 |
blue |
hold |
19, 20 |
Programming information and settings for the Siemens Sinamics G110 motor controller:
This is the same type as used in our <So> robot.
Parameter nr. |
setting |
comment |
P0003 - User Access level |
3 |
- 1= standard (motor params.)
- 2 = extended
- 3 = expert
For normal operation must be reset to 0. |
P0004 - access control filter params |
0 |
allow access to all parameters of P0003 = 3 |
P0005 - display parameter |
21 |
display motor frequency |
P0010 - commisioning params |
0 |
must be set to 1 to change motor params.
For access to P4 params and normal operation, must be set to 0
|
P0100 - Europe/ US |
0 |
= default value (Europe, 50 Hz) |
P0210 - voltage |
230 V |
mains voltage |
P0304 - nominal motor voltage |
132 V |
motor specs. (motor is triangle connected) |
P0305 - motor current |
0.56 A |
motor specs. |
P0307 - motor power |
0.07 kW |
motor specs. |
P0310 - nominal motor frequency |
50 Hz |
motor specs. |
P0311 - nominal motor rpm |
2800 |
motor specs. |
P0700 - ctrl. via control panel or digital I/O |
2 |
use digital inputs for ctrl. |
P1000 - select frequency setpoint |
2 |
set analog setpoint (1= operator panel f-ctrl) |
P1080 - min.. motor frequency |
10 Hz |
|
P1082 - max. motor frequency |
75 Hz |
|
P1120 - ramp up-time |
2" |
|
P1121 - ramp down time |
5" |
|
P2000 - max.frequency setpoint |
80 Hz |
|
P3900 - end quick commisioning |
1 |
resets P0010 |
Signals connection & pin numbering on the motor controller:
- 1 nc
- 2 nc
- 3 on/off (purple wire)
- 4 cw/ccw (nc)
- 5 fault acknowledge (grey wire)- to be used for manual reset after fault
condition.
- 6 +24 V output (pink wire)
- 7 GND (black)
- 8 +10 V output (red)
- 9 speed voltage control input (0- 10 V)
- 10 GND (black)
With the V2.0 firmware in the 18F2525 PIC controller, we get following correspondence
between the controller #7 value and the motor frequency:
Controller 7 value |
Motor frequency |
wind pressure
10 mm H20 = 1 mbar
|
remarks |
0 |
0 |
|
|
5 |
8 Hz |
|
no sound |
10 |
14 Hz |
|
motor standby, some pipes can make whistle sounds |
15 |
19.2 Hz |
|
this is the lowest limit for getting the pipes to speak |
20 |
23.6 Hz |
|
|
30 |
30 Hz |
|
pitch may be a quartertone down |
40 |
36 Hz |
|
|
50 |
40 Hz |
|
|
55 |
42 Hz |
43 mm H2O |
good for normal playing, but pitch will be a bit low |
60 |
43.7 Hz |
|
|
70 |
46.5 Hz |
|
|
72 |
47 Hz |
45 mm H2O |
this is the reference value for normal
playing, tuning and intonation. A= 440 Hz |
73 |
47.3 Hz |
|
|
75 |
47.8 Hz |
|
|
80 |
48.9 Hz |
|
|
85 |
50 Hz |
|
this would be the nominal motor frequency |
87 |
50.3 Hz |
|
|
89 |
50.5 Hz |
|
|
90 |
50.8 Hz |
|
|
95 |
51.8 Hz |
50mm H20 |
this would be the nominal pressure for the given motor. |
100 |
52.5 Hz |
|
|
110 |
54.2 Hz |
|
|
120 |
55.6 Hz |
|
|
127 |
55.7 Hz |
65 mm H20 |
|
The windpressure was measured in the windchest. The pressure measured in the
output orifices for the pipes with the valve opened is always slightly lower.
Power supply wiring: 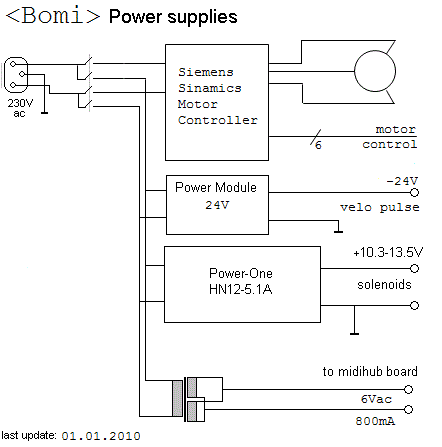
Circuit drawing for the midi-input and hub board:
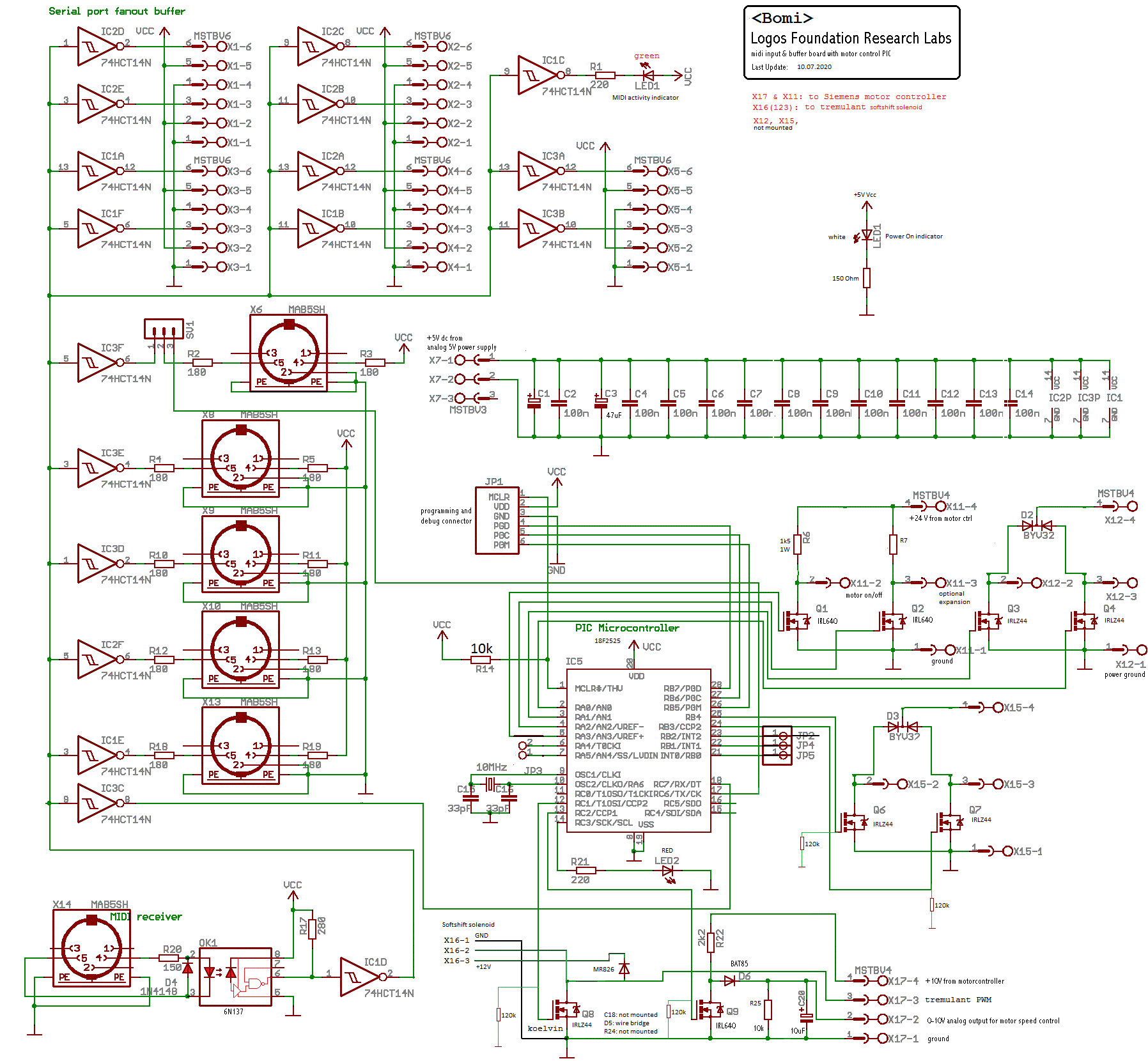
This picture can be enlarged to full size, if required.
Wiring diagram for the above board:
Parts & components:
Pipefeet: Laukhuff order numbers:2 211 09, 2 211 10, 2 211 11, 2 211 12, 2
211 13
Conical valve pallets Laukhuff order numbers: 4 091 04, 4 091 05, 4 091 06,
4 091 07
type nr |
nominal diameter |
diameter with calopel coating |
milling angle |
height |
Qty. used |
409100 |
49 mm |
50 mm |
|
|
|
409110 |
43 mm |
44 mm |
|
|
|
409101 |
38 mm |
39 mm |
|
|
|
409102 |
34 mm |
35 mm |
110° |
12.5 mm |
1 |
409103 |
29 mm |
30 mm |
|
|
|
409104 |
24 mm |
25 mm |
100° |
11 mm |
8 |
409105 |
18 mm |
20 mm |
85° |
10 mm |
10 |
409106 |
16 mm |
16.5 mm |
81° |
8.3 mm |
10 |
409107 |
12 mm |
13 mm |
72° |
7 mm |
9 |
Custom made mills: Lanoye bvba, Campus Zwijnaarde, Technologiepark 12, 9052
GENT. (091-2219337, mail: lanoye@telenet.be)
Valve solenoids: Laukhuff, 12 V type, DC resistance 80 Ohms. (the original
flat pallets have been replaced with conical ones and the springs with custom
made helical springs).
Softshift Solenoid data:
Vertical softshift solenoids for expressive wind pressure modulation mounted
inside the windchest: Ledex Softshift type 5EP (now Saia Burgess), number 193015-026.
Cold DC resistance 10.3 Ohm. Nominal working voltage at 100% duty cycle: 14
V.
- 14 V (force = 8 Newton), Current 1.36 A, Power = 19 W
- at 50% (force = 18 Newton) , 20 V, 2 A, P= 40 W
- at 25% (force= 30 Newton) , 28 V, 2.7 A, P= 75 W
- at 10%, 44 V (force= 50 Newton) , 4.3 A, P= 190 W
- Price (this is not a joke): 144 US $ a piece at Qty= 10 ...
For the working of this valve, taking into account the very low air
pressure (normally 4.5 mbar, maximum 7.0 mbar), a voltage of 12 V is enough.
The valve starts opening with a voltage of 2.6 V and is fully opened with 11
V.